Explore
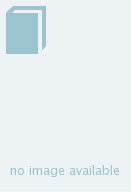
New Advances in High-Entropy Alloys
Yong Zhang (editor)
2021
0 Ungluers have
Faved this Work
Login to Fave
In recent years, people have tended to adjust the degree of order/disorder to explore new materials. The degree of order/disorder can be measured by entropy, and it can be divided into two parts: topological disordering and chemical disordering. The former mainly refers to order in the spatial configuration, e.g., amorphous alloys which show short-range ordering but without long-range ordering, while the latter mainly refers to the order in the chemical occupancy, that is to say, the components can replace each other, and typical representatives are high-entropy alloy (HEAs). HEAs, in sharp contrast to traditional alloys based on one or two principal elements, have one striking characteristic: their unusually high entropy of mixing. They have not received much noticed until the review paper entitled “Microstructure and Properties of High-Entropy Alloys” was published in 2014 in the journal of Progress in Materials Science. Numerous reports have shown they exhibit five recognized performance characteristics, namely, strength–plasticity trade-off breaking, irradiation tolerance, corrosion resistance, high-impact toughness within a wider temperature range, and high thermal stability. So far, the development of HEAs has gone through three main stages: 1. Quinary equal-atomic single-phase solid solution alloys; 2. Quaternary or quinary non-equal-atomic multiphase alloys; 3. Medium-entropy alloys, high-entropy fibers, high-entropy films, lightweight HEAs, etc. Nowadays, more in-depth research on high-entropy alloys is urgently needed.
This book is included in DOAB.
Why read this book? Have your say.
You must be logged in to comment.
Rights Information
Are you the author or publisher of this work? If so, you can claim it as yours by registering as an Unglue.it rights holder.Downloads
This work has been downloaded 135 times via unglue.it ebook links.
- 35 - pdf (CC BY) at Unglue.it.
- 100 - pdf (CC BY) at res.mdpi.com.
Keywords
- (AlCrTiZrV)-Six-N films
- (CoCrFeNi)100−xMox alloys
- ab initio
- additive manufacturing
- alloy design
- alloys design
- annealing
- annealing treatment
- atom probe tomography
- atomic-scale unstable
- AZ91D magnesium alloy
- bcc
- bulk metallic glass
- CALPHAD
- cca
- CCAs
- cluster expansion
- cluster variation method
- coating
- coherent microstructure
- complex concentrated alloys
- complex stress field
- composite
- composition scanning
- compositionally complex alloy
- compositionally complex alloys
- compressive properties
- configuration entropy
- conventional alloys
- Corrosion
- corrosion behavior
- creep mechanism
- CrFeCoNi(Nb,Mo)
- curie temperature
- deformation
- deformation and fracture
- deformation behaviors
- deformation mechanism
- density functional theory
- diamond
- differential scanning calorimetry (DSC)
- elastic property
- Electron microscopy
- elemental addition
- elemental partitioning
- elemental powder
- elevated-temperature yield strength
- elongation prediction
- Entropy
- eutectic dendrites
- first-principles calculation
- First-principles calculations
- flow serration
- gamma double prime nanoparticles
- graded material
- grain refinement
- Hall–Petch (H–P) effect
- hardening behavior
- hardness
- HEA
- HEAs
- heat-softening resistance
- hierarchical nanotwins
- high entropy alloy
- high entropy alloys
- high pressure
- high-entropy alloy
- high-entropy alloy coating
- high-entropy alloys
- high-entropy alloys (HEAs)
- high-entropy ceramic
- high-entropy film
- high-entropy films
- high-pressure torsion
- high-temperature structural alloys
- immiscible alloys
- in situ X-ray diffraction
- interface
- interstitial phase
- ion irradiation
- kinetics
- laser cladding
- laser metal deposition
- lattice constants
- lattice distortion
- lightweight alloys
- liquid phase separation
- low-activation alloys
- low-activation high-entropy alloys (HEAs)
- Magnetic properties
- magnetic property
- matrix formulation
- Maximum entropy
- mechanical alloying
- mechanical behaviors
- mechanical characterization
- Mechanical properties
- Mechanical Property
- medium entropy alloy
- medium entropy alloys, mechanical properties
- metal matrix composites
- microhardness
- microstructural evolution
- Microstructure
- microstructures
- miscibility gaps
- Monte Carlo
- MPEAs
- multi-principal element alloys
- multicomponent
- multicomponent alloys
- nanocomposite structure
- nanocrystalline
- Nanocrystalline Materials
- nanodisturbances
- nanoprecipitates
- nanoscaled high-entropy alloys
- partial recrystallization
- phase composition
- phase constituent
- phase constitution
- phase evolution
- phase stability
- phase structures
- phase transformation
- phase transformations
- phase transition
- Plasticity
- plasticity methods
- polymorphic transition
- powder metallurgy
- precipitation
- precipitation kinetics
- recrystallization
- Reference, information & interdisciplinary subjects
- refractory high entropy alloys
- refractory high-entropy alloys
- Research & information: general
- scandium effect
- serration behavior
- shear band
- sodium chloride
- solid solution strengthening effect
- solid-solution
- solid-solution alloys
- solid-state diffusion
- solidification
- spark plasma sintering
- specific heat
- sputtering
- stacking-fault energy
- strain rate sensitivity
- strengthening
- strengthening mechanisms
- structural metals
- sulfuric acid
- tensile creep behavior
- tensile strength
- thermal expansion
- thermodynamic Integration
- thermoelectric properties
- Thin films
- transmission electron microscopy
- volume swelling
- wear
- wear behaviour
- Welding
Links
DOI: 10.3390/books978-3-03943-620-0Editions
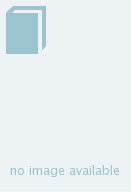