Explore
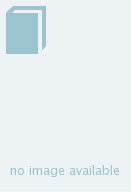
Finishing Operations to Enhance Surface Integrity of Parts
0 Ungluers have
Faved this Work
Login to Fave
Surface integrity management is remarkably important when metal alloys are used to manufacture relevant parts. Advanced materials such as titanium, nickel alloys, non-ferrous alloys, or special steels make surface integrity preservation after machining particularly difficult. Consequently, thorough finishing techniques are required to rectify the surface integrity. Engineering surfaces that exemplify the importance of surface integrity control are typically found in the transportation industry. Pieces formed using complex curved surfaces, such as turbine blades or landing gears, and molds and dies for upsetting operations are good examples. These kinds of parts are often manufactured through 3- or 5-axis machining with the aid of successive adjacent passes of hemispherical tools, whereas this ball-end milling strategy allows one to achieve complex surfaces by following the desired shape through NC interpolations generated by a CAM (it also has deep constraints). In this context, processes such as burnishing, honing, plateau-honing, grinding, and shot-peening can contribute to improving the described surfaces in terms of texture, residual stress, and hardness, and are easily maneuverable from a procedural point of view. This Special Issue collected the research results on these kinds of finishing processes, which are very important to the transportation industry.
This book is included in DOAB.
Why read this book? Have your say.
You must be logged in to comment.
Rights Information
Are you the author or publisher of this work? If so, you can claim it as yours by registering as an Unglue.it rights holder.Downloads
This work has been downloaded 61 times via unglue.it ebook links.
- 61 - pdf (CC BY) at Unglue.it.
Keywords
- AA2024 floor milling
- abrasive shot blasting
- accelerometer
- acoustic emission
- additive manufacturing
- austenitic stainless steel
- ball burnishing
- Bayesian rule
- bearing steel
- chatter
- desirability function
- fatigue life
- finish milling
- finishing operations
- finishing processes
- friction coefficient
- fused filament fabrication
- History of engineering & technology
- honing
- laser scanning
- laser sensors
- material removal rate
- microhardness
- mixture design
- natural frequencies
- non-contact metrology
- operational deflection shape
- optimization
- part quality
- PEI Ultem 9085
- piezoelectric
- positron mean lifetime τmean
- postprocessing
- precision spheres
- process monitoring
- regular reliefs
- residual stress
- residual stresses
- rolling contact fatigue
- roughness
- sandblasting
- sensitivity analysis
- shot peening
- slide burnishing
- Stainless Steel
- surface enhancement
- surface integrity
- surface roughness 3D
- surface topography
- t-test
- Technology, engineering, agriculture
- Technology: general issues
- thermal annealing
- tool wear
- topography
- tribological interaction
- tribology
- ultrasonic
- vapor smoothing
- vibration-assisted ball burnishing
- X6CrNiTi18 stainless steel
Links
DOI: 10.3390/books978-3-0365-9285-5Editions
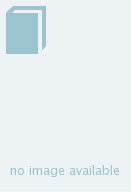