Explore
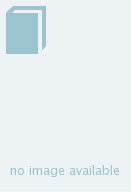
Advances in Ultra-Precision Machining Technology and Applications
Benny Cheung (editor) and Jiang Guo (editor)
2024
0 Ungluers have
Faved this Work
Login to Fave
Ultra-precision machining technology has been widely used in the manufacture of many mission-critical components for various industrial areas, such as advanced optics, photonics aerospace, the automotive industry, telecommunications, biomedical areas, energy, the environment, etc. Nowadays, ultra-precision machining technology is capable of producing workpieces with submicron shape accuracy, nanometer surface roughness, and high geometric complexity. Due to increasing geometrical complexity, high-precision requirements and the evolution of advanced materials of the workpiece being machined lead to numerous research challenges in different fields, including ultra-precision machining technologies, novel machining processes, cutting mechanics, surface generation mechanisms, novel machine design, advanced sensing, and machine metrology. In addition, the machining process can be accurately controlled through the modeling and simulation of ultra-precision machining processes, error compensation, materials sciences, measurement and on-machine metrology, as well as advanced applications for functional uses. This reprint aims to collate the latest research results on ultra-precision machining technology and applications in order to promote the development of related industrial technology with high efficiency, high precision, and intelligence.
This book is included in DOAB.
Why read this book? Have your say.
You must be logged in to comment.
Rights Information
Are you the author or publisher of this work? If so, you can claim it as yours by registering as an Unglue.it rights holder.Downloads
This work has been downloaded 39 times via unglue.it ebook links.
- 39 - pdf (CC BY-NC-ND) at Unglue.it.
Keywords
- 6H-SiC
- accuracy
- aerostatic spindle
- Al6061
- capacitive sensor
- chip morphology
- clamping error
- computational efficiency
- computational fluid dynamic study
- computer-aided innovation
- cutting error
- cutting force
- cutting-edge radius
- delay-differential equation
- difficult-to-machine material
- dry etching
- dry polishing
- duty ratio
- dynamic stiffness and damping
- dynamics modeling
- electrochemical machining
- empirical mathematical model
- Erosion
- error compensation
- error sources analysis
- fast tool servo
- feed rate
- FEM
- femtosecond laser
- finite element analysis
- finite element simulation
- fixed abrasive
- Floquet theory
- fluid flow
- friction coefficient
- gas–liquid two-phase flow
- high frequency
- hydrostatic guideways
- inlet pressure
- innovation design
- interaction mechanism
- knowledge-based engineering
- lateral gap
- machining methods
- Measurement
- Mechanism
- micro-turbine
- microchanges
- micromachining
- Milling stability
- MOEMS
- motion errors
- multi-physical field coupling simulation
- multifocal microlens array
- n/a
- optical glass
- partial porous orifice
- Period
- phase transition temperature
- potassium dihydrogen phosphate (KDP) crystal
- precision shafting
- Problem solving
- processing voltage
- Reynolds equation
- rotor trajectory
- shear angle
- silicon microcantilever
- single point diamond fly-cutting
- single-particle erosion
- Smart Manufacturing
- smoothed particle hydrodynamics
- solid-phase oxidant
- spherical steel mould
- Stability
- stress concentration depth
- subsurface damage
- surface layer
- thermal error
- tribochemical mechanical polishing
- ultra-precision machining
- ultraprecision lapping
- ultrasonic-assisted vibration cutting
- weak-stiffness mirror
- wear
Links
DOI: 10.3390/books978-3-7258-1559-3Editions
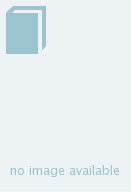